Lean is a structured system based on continuous improvement and customer satisfaction.
“The Lean Thinking,” derived from the principles of Lean manufacturing, has subsequently been expanded to various fields such as software development and project management.
Continuous improvement is the adaptation of Lean Six Sigma in 5 steps: DMAIC.
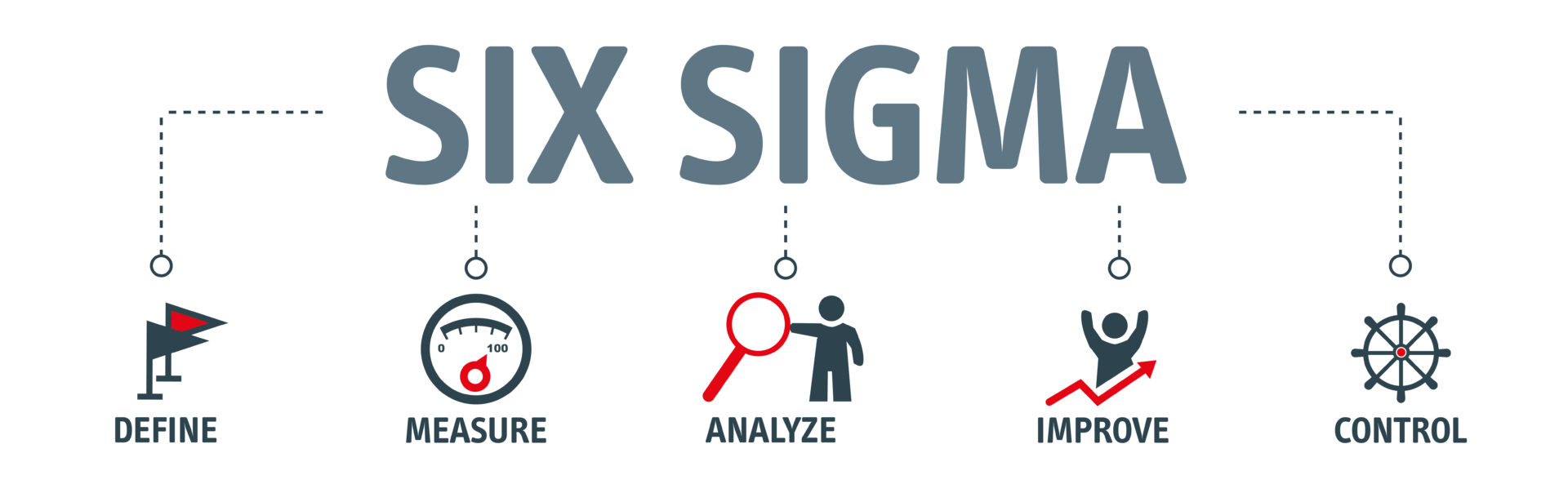
- -Define : sets the context
- -Measure the gaps
- -Analysis of current and past data
- – Improve : solves the problem
- – Control : check your solution and verify that it corrects the problem.
In game coaching and facilitation, it is visual management that will be the primary objective of the Lean system.
This sheet aims to show the extent of the Lean system and not the animation tips.
Lean is a structured system based on continuous improvement and customer satisfaction
Over the past 30 years, as part of the Lean movement or other trends in management, organization and quality: these two concepts have been widely developed and implemented around the world in all kinds of variations, tools and methods.
Il est toutefois certain que, des nombreuses entreprises qui ont entendu parler du Lean, ont pensé au Lean ou essayé le Lean, bien peu ont poursuivi efficacement cet axe de progrès. Recruter quelques ingénieurs ou managers expérimentés dans le domaine, former les collaborateurs à la mise en œuvre des outils, utiliser des consultants pour lancer un chantier Kaizen (amélioration continue) ne font pas une entreprise Lean.
However, it is certain that, of the many companies that have heard of Lean, have thought of Lean or tried Lean, very few have effectively pursued this direction for improvement. Recruiting a few engineers or managers with experience in the field, training employees in the implementation of tools, using consultants to launch a Kaizen project (continuous improvement) does not make a Lean company.
Progress is rapid and generally visible, but efforts often slow down when there is a change in management, direction or under the impetus of a new consulting firm deploying another progress strategy.
Beyond the Lean tools and principles, all of which are proven and effective, there is their implementation in the company.
The Lean system: what context?
First, every business is as unique as its leaders, its people and its history. Therefore, tools and methods do not have to be applied “as is” to be effective. What applies to Toyota will certainly not apply to your company, for example because of the size difference. Thus, it is necessary to adapt them according to the specificity of your company and its internal and external environment.
Then, a business is a collection of people who “make” the business by creating the added value that its customers buy. Therefore, the Lean system is available to all employees: from the manager to the sweeper. A sustained and effective Lean approach over time requires the involvement of ALL of the company’s employees.
The involvement of everyone is the key to a successful Lean system deployment. This is what Toyota calls developing talent and it is one of the major strategic axes of the company.
The Lean system is based on visual sharing of information
The “technical” foundations of the Lean system are visual management (simplification and total transparency of actions) and stable and standardized processes (in order to be able to improve them and correct problems “scientifically”). A number of tools and methods allow these foundations to be solidly built and then extended as the business grows.
Without these solid foundations, the implementation of the tools and techniques of the two pillars of just in time (JIT) and quality at the heart of processes (JIDOKA) will not give all the expected results (progress in performance over time). ) if the Lean culture is not found at all levels of the company.
What are the conditions for implementing a Lean system?
Having standardized and stable processes is essential for effective improvement processes and problem solving.
The Lean system invites you to record and classify field observations.
To do this, it will use tools such as the PDCA (Plan Do Check Act) used in conjunction with the A3, which is the summary format used to note and classify observations and the resolution of anomalies – and thus verify in the field that the initial situation is properly documented and stabilized.
Basically, you have to observe in order to be able to see. Problems, anomalies, waste … that we do not see will not be solved or eliminated. And the observation always happens where the value is created, on the ground with the people who create that value. Lean being applicable to all areas and all companies, the field (Gemba) is just as much the workshop as the shipping area, the design office, offices, treatment rooms, in short, wherever customer purchased value is created.
Advantage and drawback of the Lean system
The Lean system has the advantage of: Focusing on creating value, eliminating waste by always developing the talent of its employees to better satisfy its customers and prepare to acquire new ones.
The Lean system is often rejected and controversial because resolving anomalies and streamlining processes allows production downsizing.
Moreover LEAN means to LOSE WEIGHT in the light sense to simplify.
This unpopularity left room for the deployment of the Agile system.
The popularity of Agile values and their deployment at scale makes the Agile system fragile in turn because it is now associated with an improvement in production times and a return to hellish rates so well illustrated by Charlie Chaplin in modern times.
Moreover, the strongest critics of Agile values are often found in autocratic management and Lean management.
To find out more about the components of management over time, discover our strategic management section
A Lean system that enabled an industry to simplify its manufacturing processes and cut out the functions of each, will be the basis for that same industry of the success of a Digital Factory.
The resolutely customer-centric Digital Factory will naturally accept Agile values a direction for improvement and will promote the emergence of team autonomy.
Author: Dominique Popiolek-Ollé, Transmutation leader, Agile Executive Coach, Founder of In Imago, management consulting and disruptive transformation.